Lukashchuk et al. recently published a paper titled "Photonic-electronic integrated circuit-based coherent LiDAR engine" in the journal Nature Communications.
Open access link: https://www.nature.com/articles/s41467-024-47478-z
Abstract: Chip-scale integration is a key enabler for the deployment of photonic technologies. Coherent laser ranging or FMCW LiDAR, a perception technology that benefits from instantaneous velocity and distance detection, eye-safe operation, long-range, and immunity to interference. However, wafer-scale integration of these systems has been challenged by stringent requirements on laser coherence, frequency agility, and the necessity for optical amplifiers. Here, we demonstrate a photonic-electronic LiDAR source composed of a micro-electronic-based high-voltage arbitrary waveform generator, a hybrid photonic circuit-based tunable Vernier laser with piezoelectric actuators, and an erbium-doped waveguide amplifier. Importantly, all systems are realized in a wafer-scale manufacturing-compatible process comprising III-V semiconductors, silicon nitride photonic integrated circuits, and 130-nm SiGe bipolar complementary metal-oxide-semiconductor (CMOS) technology. We conducted ranging experiments at a 10-meter distance with a precision level of 10 cm and a 50 kHz acquisition rate. The laser source is turnkey and linearization-free, and it can be seamlessly integrated with existing focal plane and optical phased array LiDAR approaches.
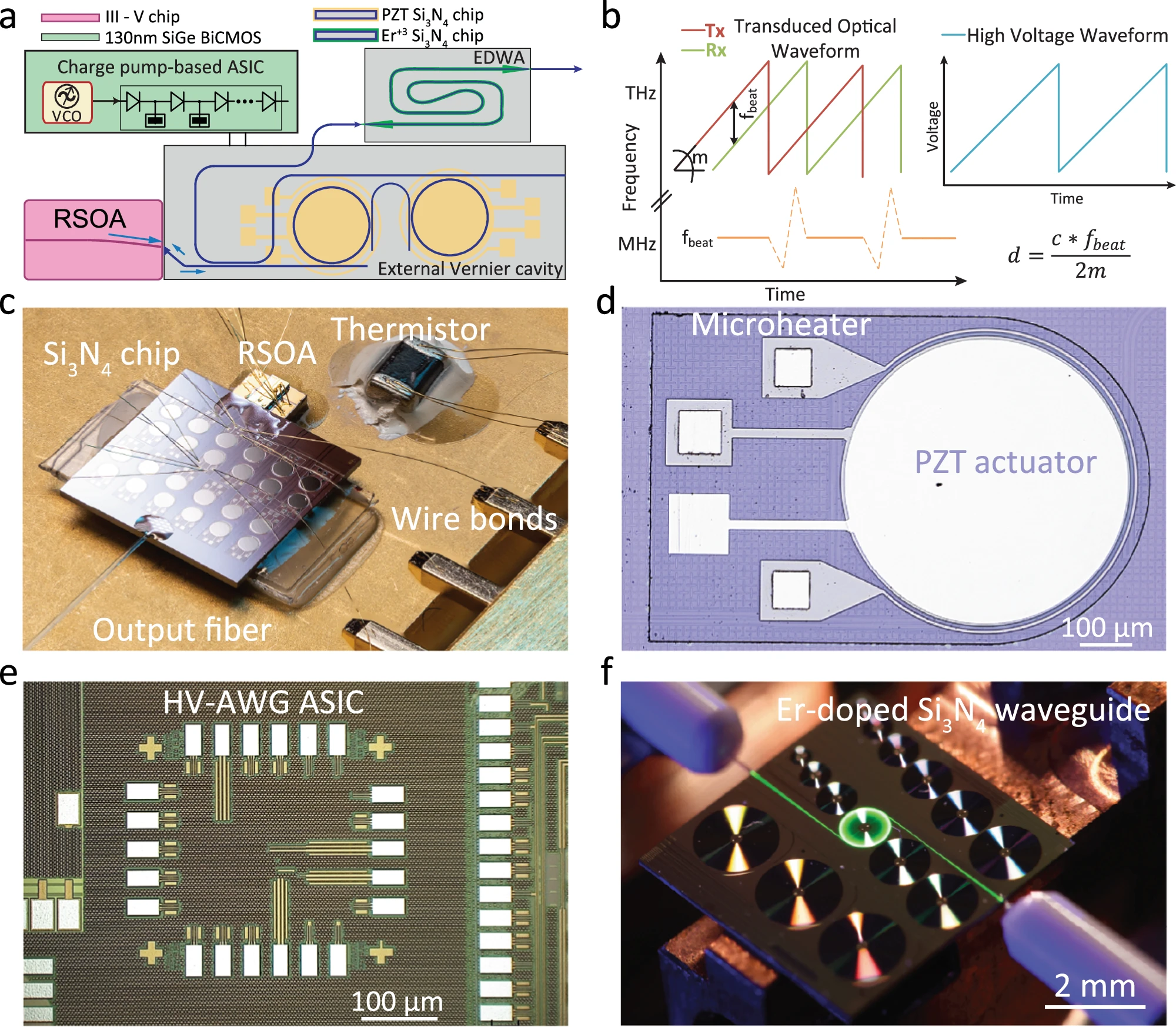
a Schematics of photonic-electronic LiDAR structure comprising a
hybrid integrated laser source, charge-pump based HV-AWG ASIC, photonic
integrated erbium-doped waveguide amplifier. b Coherent ranging principle. c Packaged laser source. RSOA is edge coupled to Si3N4
Vernier filter configuration waveguide, whereas the output is glued to
the fiber port. PZT and microheater actuators are wirebonded as well as
butterfly package thermistor. d Zoom-in view of (c) highlighting a microring with actuators. e Micrograph of the HV-AWG ASIC chip fabricated in a 130 nm SiGe BiCMOS technology. The total size of the chip is 1.17–1.07 mm2. f
The Erbium-doped waveguide is optically excited by a 1480 nm pump
showing green luminescence due to the transition from a higher lying
energy level to the ground state.
a Schematics of the integrated circuit consisting of a 4-stage
voltage-controlled differential ring oscillator which drives charge pump
stages to generate high-voltage arbitrary waveforms.
b
Principles of waveform generation demonstrated by the output response to
the applied control signals in the time domain. Inset shows the change
in oscillation frequency in response to a frequency control input, from
88 MHz to 208 MHz, which modifies the output waveform.
c Measured arbitrary waveforms generated by the ASIC with different shapes, amplitudes, periods and offset values.
d Generation of the linearized sawtooth electrical waveform used in LiDAR
measurements. Digital and analog control signals are modulated in the
time domain to fine-tune the output.
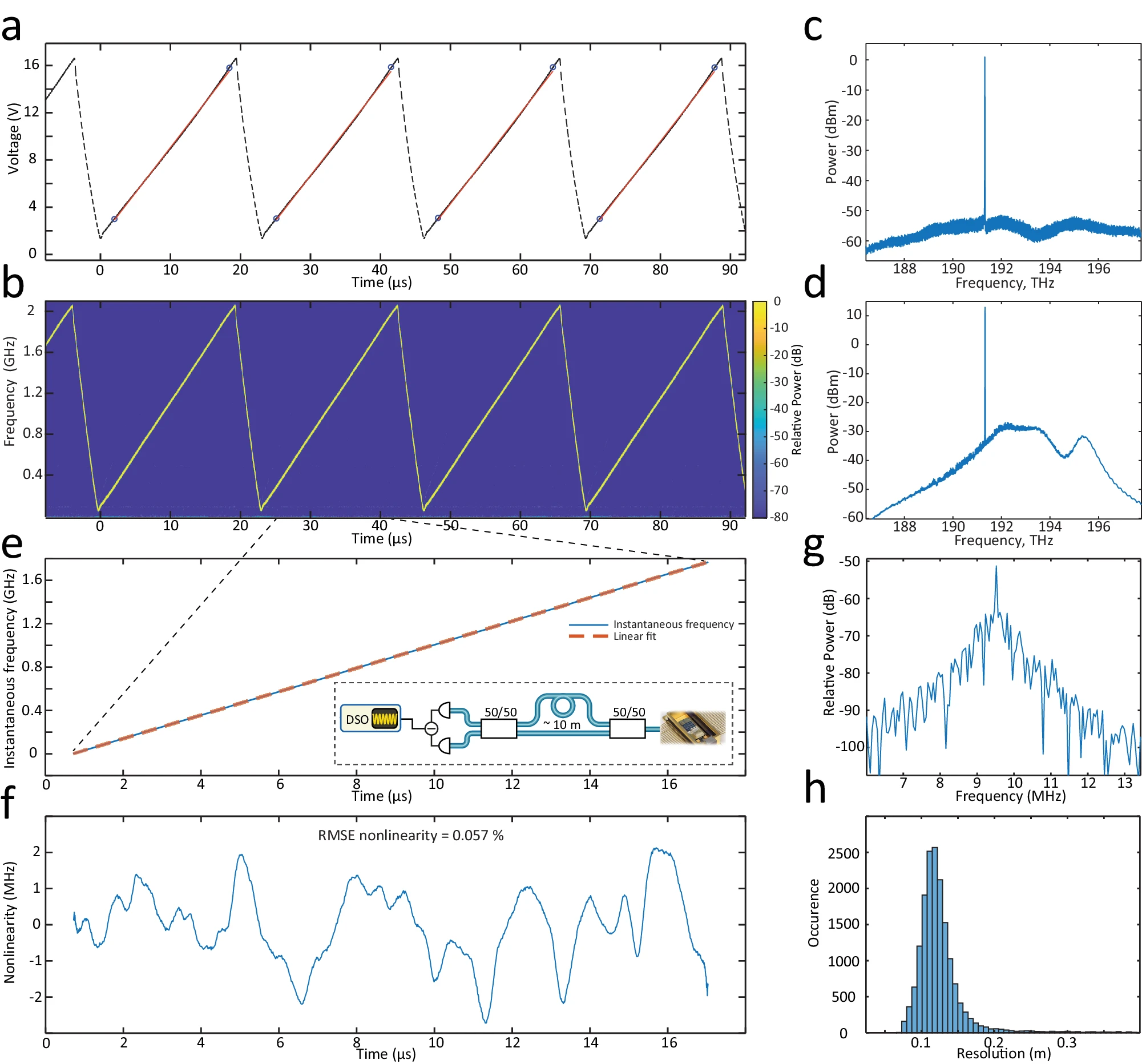
a Electrical waveform generated by the ASIC. Blue circles highlight the segment of ~ 16 μs used for ranging and linearity analysis. The red curve is a linear fit to the given segment. b Time-frequency map of the laser chirp obtained via heterodyne detection with auxiliary laser. RBW is set to 10 MHz. c Optical spectrum of Vernier laser output featuring 50 dB side mode suppression ratio. d Optical spectrum after EDWA with >20 mW optical power. e
Instantaneous frequency of the optical chirp obtained via delayed
homodyne measurement (inset: experimental setup). The red dashed line
corresponds to the linear fit. The excursion of the chirp equates to
1.78 GHz over a 16 μs period. f Nonlinearity of the laser chirp inferred from (e). RMSE nonlinearity equates to 0.057% with the major chirp deviation from the linear fit lying in the window ± 2 MHz. g
The frequency beatnote in the delayed homodyne measurement corresponds
to the reference MZI delay ~10 m. The 90% fraction of the beatnote
signal is taken for the Fourier transformation. h LiDAR
resolution inferred from the FWHM of the MZI beatnotes over >20,000
realizations. The most probable resolution value is 11.5 cm, while the
native resolution is 9.3 cm corresponding to 1.61 GHz (90% of 1.78 GHz).
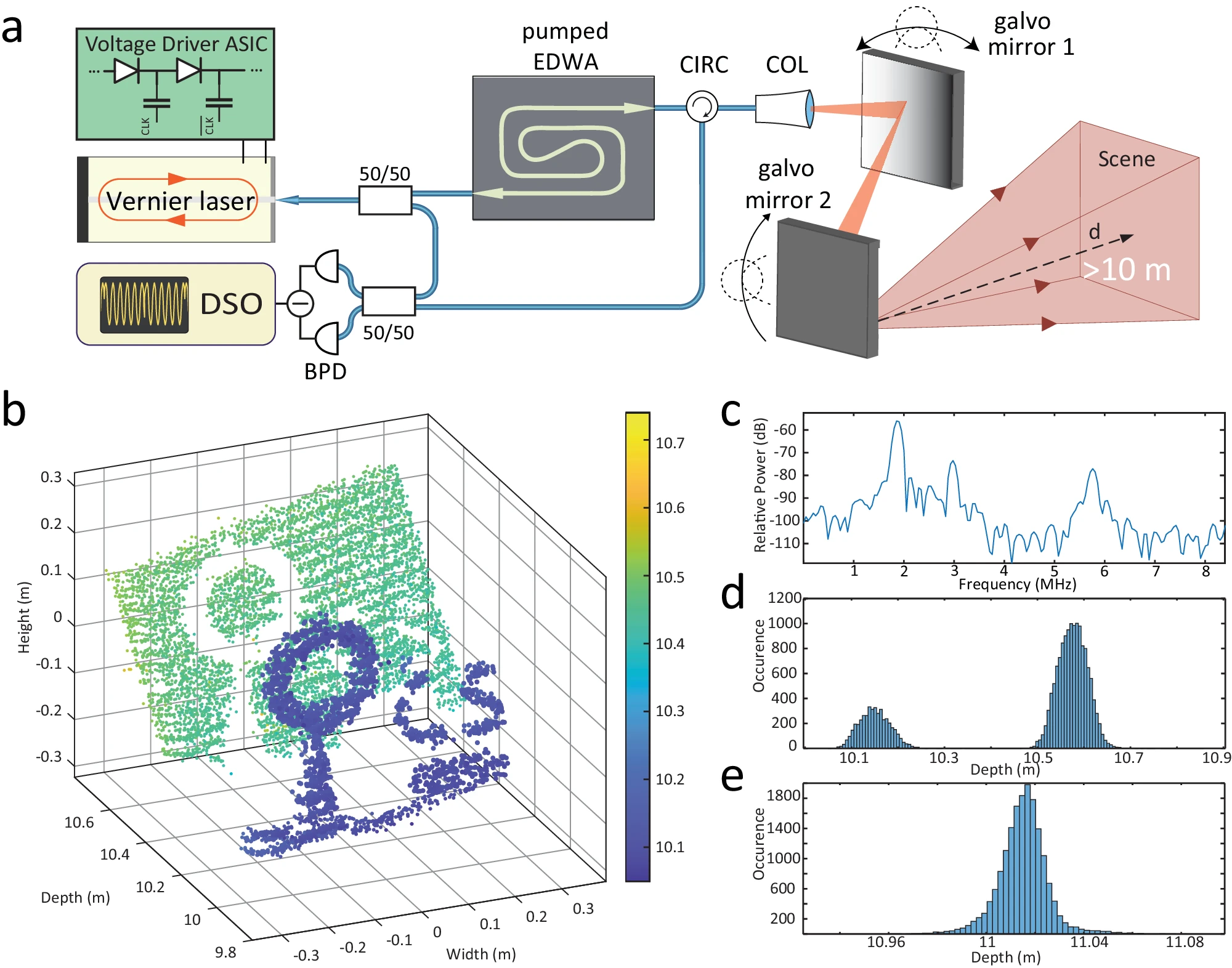
a Schematics of the experimental setup for ranging experiments.
The amplified laser chirp scans the target scene via a set of galvo
mirrors. A digital sampling oscilloscope (DSO) records the balanced
detected beating of the reflected and reference optical signals. CIRC -
circulator, COL - collimator, BPD - balanced photodetector.
b Point cloud consisting of ~ 10
4 pixels featuring the doughnut on a cone and C, S letters as a target 10 m away from the collimator.
c
The Fourier transform over one period, highlighting collimator,
circulator and target reflection beatnotes. Blackman-Harris window
function was applied to the time trace prior to the Fourier
transformation.
d Detection histogram of (
b).
e Single point imaging depth histogram indicating 1.5 cm precision of the LiDAR source.